1.材料管理
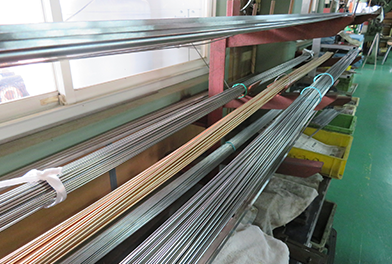
メッキ治具の形状に加え、材料の選定も重要です。表面処理、洗浄や塗装等では使用される環境が違うので材料も変わります。使用頻度、使用期間、搬送方法、ワーク重量、トータルコスト等を考慮した上で材料を決定し、系統立った材料管理を行い、自社管理システムで必要素材の補充を行いニーズにお応えする体制を維持しています。
2.切断
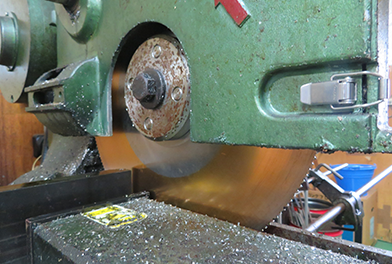
メッキ治具は、棒形状の材料の組み合わせで構成されることが多いのですが、切断の精度、角度によって棒形状の集合体であるラックの形状にも影響が出ます。丁寧に切断を行うことが良いラック製造の基本となり、当社では自動ワイヤーホーミング(コンピュータ制御による線材加工)により安定した切断工程を実現しています。
3.加工
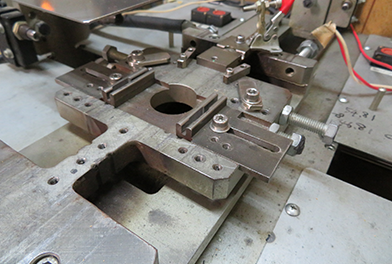
曲げ加工はデリケート作業であり、治具は「しっかりしたホールド+処理後はワークが外れやすい」ことが必須です。経験値の蓄積や熟練技を伴う加工であり、数値化できない少しの変化が治具の形成に生かされます。材料は主に切断→穴あけ→曲げ加工→スポット溶接等の工程で形成されます。
4.組立溶接
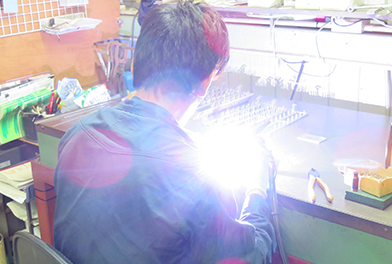
切断、曲げ加工等の工程で丁寧な材料が揃っていても、溶接時の取り付け角度が変わるだけで使用時に不具合が発生します。この工程も職人的要素が多い専門的工程で、治具製造の要の工程です。治具製造では同じような作業を根気よく、正確に作業し続ける必要があり、組立工程は集中力を持続する作業となります。
5.コーティング
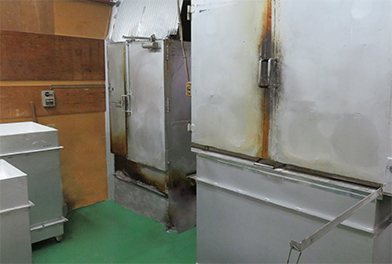
組立・溶接工程を経て出来上がってきた治具は、必要に応じたコーティング処理が施されます。腐食性の強い薬品の環境下で使用される治具に樹脂コーティングは必要不可欠。複雑な形状になりがちな治具のコーティングで均一な皮膜を形成するために当社では独自の製造装置を開発し完全な皮膜作りを実現します。
6.完成
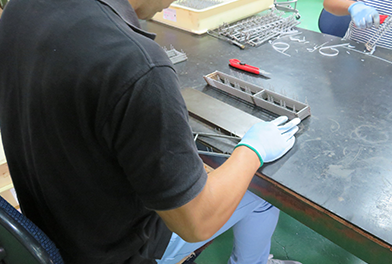
コーティングが施された治具からコーティングが不要な部分の皮膜を切り取ったり、バリ取りや端部処理などのサンディングを行う工程です。全般的なチェックを丹念に行い、出荷に備えます。